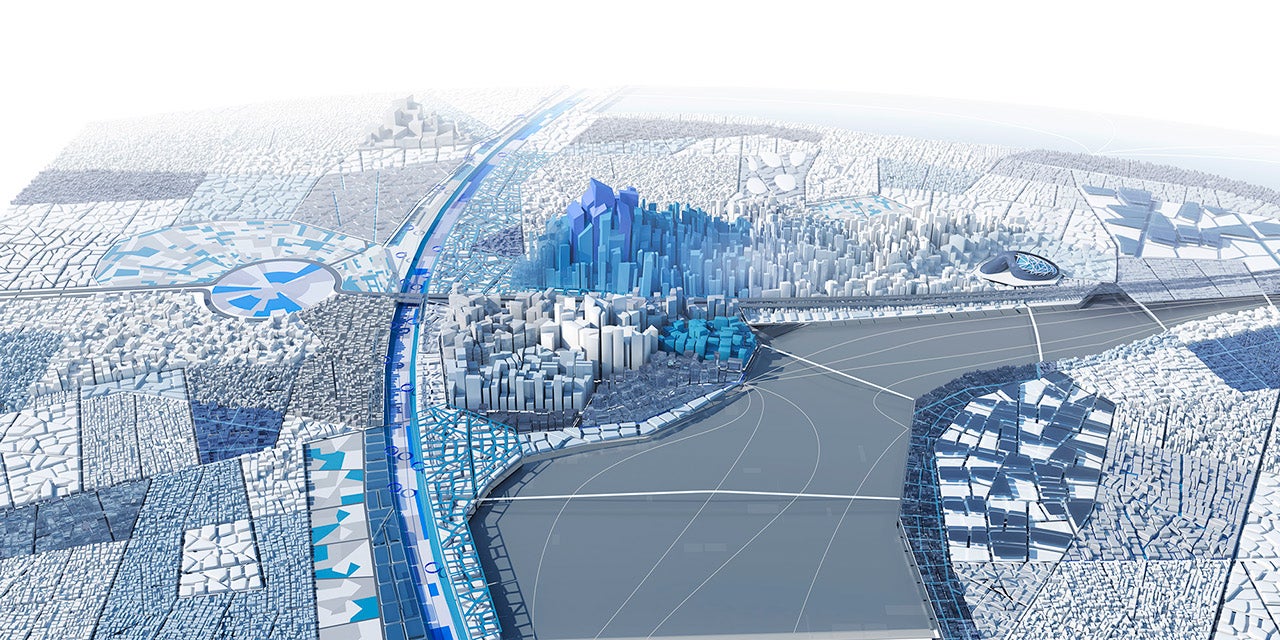
Factory operators face a variety of challenges that affect their operations these days. These challenges require a strategic approach and investment in technology, smart resource management and human resource development.
Whether planning a new factory or optimizing an existing plant, factory operators face various challenges today, but also have more (digital) options than ever before.
Investing in a digital factory pays off as it increases efficiency, minimizes errors, reduces costs and thus improves competitiveness. Digital solutions simplify the planning, monitoring and control of the production process in particular, but also plant management, which ensures the functionality of machines and systems, as well as occupational safety in general.
With the help of digital factory software, operators can test various scenarios in advance, minimize downtimes and improve maintenance processes. This leads to higher productivity, lower costs and a better basis for decision-making for the entire life cycle of the factory, including all machines and installations.
Overall, there is a wide range of digital possibilities to turn your plant into a smart factory. Cideon offers a wide range of services for innovative solutions to support factory and plant operators. With our expertise and technologies, we enable real-time monitoring and efficient operations. We support the implementation of digital twins for optimized production and higher added value. With a holistic view of the data, we integrate buildings, building technology and production systems into a consistent model. Our solutions help factory operators and plant constructors to learn from their data and make informed decisions to continuously improve their operations.
You can rely on our decades of experience in industrial environments. We will be happy to advise you on which solutions are best suited to your individual situation.
Factory operators face a variety of challenges that affect their operations these days. These challenges require a strategic approach and investment in technology, smart resource management and human resource development.
In order to effectively meet the current challenges facing factory operators and plant constructors, sustainable solutions for the digital factory are essential. In the following illustration, you can see what makes a factory a smart factory.
Factory operators face complex challenges in a constantly changing industrial landscape. Innovative and digital solutions as well as smart factory software are crucial for securing and increasing efficiency and competitiveness in the long term and optimizing cooperation with machine building and plant construction companies.
Digitalization offers factory operators a wide range of benefits, from increased efficiency and cost savings to improved production planning and faster response times to meet changing market demands. Discover the advantages of a virtual factory now.
Discover software solutions for the optimization of your factory. Create more precise layouts, share your designs with everyone involved in the project and benefit from a better data base. Here you will find an overview of specialized smart factory software.
Factory operators are facing global challenges such as supply chain complexity, digital transformation, sustainability goals and a shortage of qualified employees. These require strategic adjustments for competitiveness and sustainability.
A digital factory integrates advanced technologies to optimize production processes. Automation, connectivity and real-time data enable efficient production and resource utilization.
A digitalized factory optimizes production processes through automation, simulation options, data analysis and connectivity. This results in greater efficiency, reduced costs, better planning, improved resource management, faster time to market and increased competitiveness. Real-time data also enables precise decision-making and the promotion of innovation.
Industry 4.0 is central to the digital factory. It integrates intelligent technologies to connect and optimize production processes. This transformation enables more efficient, flexible and adaptable manufacturing processes, promotes innovation and increases competitiveness. Industry 4.0 is revolutionizing the way factories work and paving the way for advanced, highly automated production.
The digital twin plays a central role for the digital factory, as it enables a virtual representation of physical systems. This includes real-time monitoring, simulation of processes and precise analyses. Factory operators can increase efficiency, improve maintenance and minimize downtime, resulting in overall optimized production. The digital twin simplifies decision-making and enables proactive adaptation to changes in the real factory environment.
The terms “digital factory” and “smart factory” are often used synonymously, but can have slightly different focuses.
The digital factory emphasizes the integration of digital technologies to optimize production processes, while the smart factory presents a broader context.
A smart factory not only integrates digital technologies, but also uses comprehensive connectivity, real-time data, artificial intelligence and IoT to create a highly autonomous, self-controlling and flexible production environment.
Cideon advises and supports companies in optimizing their product development processes - from conception and engineering to production and service. We stand for:
CIDEON Software & Services GmbH & Co. KG
Lochhamer Schlag 11, 82166 Gräfelfing (Germany)