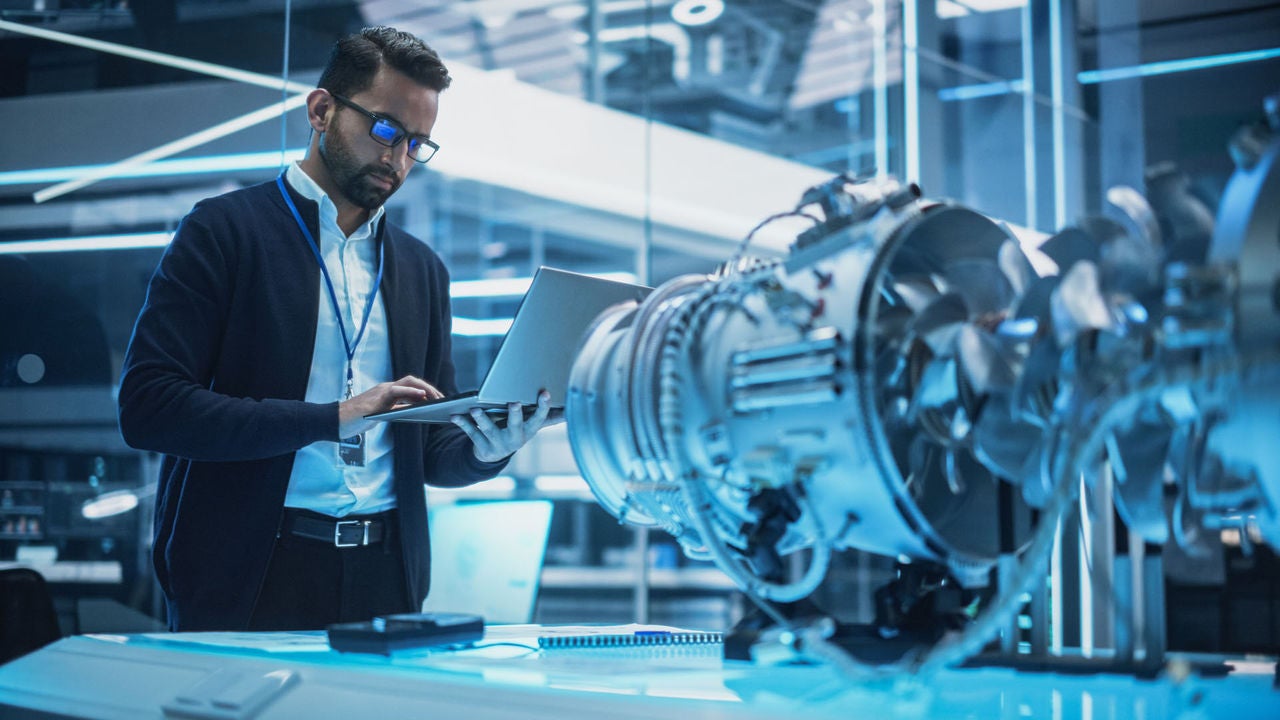
Integrated SAP ERP/PLM Solution for a Breath of Fresh air in Blower and Compressor Technology
A single source of truth across the complete product development process provides better data quality and allows consistent reuse of engineering data for purchasing, distribution, and manufacturing. To reap these benefits, organizations require not only an integrated ERP/PLM system, but also a competent partner to support the implementation project from beginning to end—a partner that is in a position to provide broad-based support for the optimization of their business processes. According to Axel Stürmer, director of the engineering company’s PLM project, AERZEN has found such a partner in Cideon.